Faserverbundwerkstoffe wie beispielsweise kohlenstofffaserverstärkte Kunststoffe (CFK, oder kurz: Carbon) sind rund 30 Prozent leichter als Aluminium und zugleich fester als Stahl. Zudem rostet das Material nicht. Ihre Stabilität erhalten die Materialien durch Kohlenstofffasern, die in eine Kunststoffmatrix eingebettet sind. Dem Hightech-Werkstoff, der bereits in der Luft- und Raumfahrt sowie im Automobilbereich eingesetzt wird, gehört zweifellose die Zukunft. Allerdings muss die Produktion (bislang größtenteils aufwendig und teuer in Manufakturen) noch erheblich effizienter werden und auch das Recycling der Werkstoffe bereitet noch Probleme, auch wenn in beiden Bereichen innerhalb des letzten Jahres schon deutliche Fortschritte erreicht wurden (siehe Links unten). Bis 2020 dürften der Markt laut Roland Berger Strategy Consulting um 17 Prozent jährlich wachsen und die Kosten um 30 Prozent zurückgehen. Ein weiterer bedeutender Fortschritt ist nun Fraunhofer-Forschern gelungen: Sie haben es erstmals geschafft, die RFID-Technologie auch in Faserverbundwerkstoffe zu integrieren.
RFID (engl. radio-frequency identification / Identifizierung mit Hilfe elektromagnetischer Wellen) wird vor allem in der Logistik und in der Produktion eingesetzt. Die in die Werkstoffe oder die Verpackung integrierten RFID-Transponder (umgangssprachlich auch Funketiketten genannt) ermöglichen dabei die automatische Identifizierung und Lokalisierung von Gegenständen und damit die Erfassung von Daten, z.B. Frachtdaten in der Logistik oder Daten zu den einzelnen Produktionsschritten in der Produktion (Qualitätssicherung).
Aus der Bekanntmachung des Fraunhofer IIS
Antennen, die Radiowellen weiterleiten können, verwandeln Bauteile in intelligente Objekte. Forscher haben jetzt einen Weg gefunden, diese auch in Faserverbund-werkstoffe einzubetten. Damit funktioniert die Technologie auch bei Kohle- und Glasfasern.
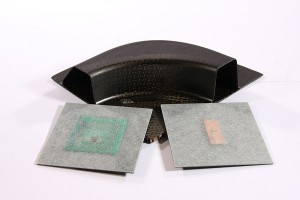
© TUM-IWB / Fraunhofer IIS
Mit bloßem Auge ist es nur schwer zu erkennen. Die Werkstücke in der Produktionshalle sehen eigentlich ganz normal aus. Doch der erste Blick täuscht. Die Flugzeug- bauteile sind »intelligent« und können mit den anwesenden Facharbeitern kommunizieren. Sie verraten nicht nur was sie sind, sondern auch, wer sie bisher wie bearbeitet hat und welcher Arbeitsschritt als nächstes ansteht. Quelle des Informationsflusses ist ein kleiner RFID-Chip (radio-frequency identification). Er misst nur wenige Quadrat- millimeter und sendet schnell, effizient und konsistent Daten des Bauteils über Radiowellen an ein Empfangs- gerät. Bislang setzen wenige Unternehmen die Technologie zur Dokumentation in der Fertigung ein. Am häufigsten nutzen sie RFID für die Zugangskontrolle oder zur Zeiterfassung, zum Beispiel in den Smartcards der Mitarbeiter.
Wie gut ein RFID-Transponder funktioniert, hängt maßgeblich vom umgebenden Werkstoff ab. Dieser kann die Antennen der Transponder beeinflussen und sich negativ auf die Reichweite sowie die Qualität der Datenübertragung auswirken. Forscher am Nürnberger Standort des Fraunhofer-Instituts für Integrierte Schaltungen IIS haben jetzt RFID-Trans- ponder entwickelt, deren Antennen auch auf Faserverbundwerkstoffen zuverlässig funktionieren. Bauteile aus Glas- oder Kohlefaser sind leicht und stabil zugleich und werden daher vor allem beim Flugzeug- und Fahrzeugbau immer häufiger eingesetzt. Doch die Fasern beeinflussen die Frequenzen besonders stark. Ihr genaues Verhalten gegenüber RFID war bisher kaum bekannt. Die Dokumentation der Produktionsschritte läuft daher immer noch mit Bleistift und Papier.
Kohlefasern schwächen Leistung der RFID-Chips
»Wir haben uns die für die RFID-Technologie relevanten Frequenzen 125 kHz (LF: low frequency), 13,56 MHz (HF: high frequency) und 868 MHz (UHF: ultra high frequency) genau angesehen und gemessen, wie sich Glas- und Kohlefasern auf die Reichweite, die Datenübertragung und die Zuverlässigkeit der Transponder auswirken«, beschreibt Diplom-Ingenieur Tobias Dräger die Arbeiten am IIS. Das Ergebnis: Während sowohl LF, HF und UHF an Glasfasern gut funktionierten, schwächten bei Kohlefasern insbesondere die hohen Frequenzen die Leistung der RFID-Chips deutlich ab. »Kohlefasern sind, ähnlich wie Metall, leitfähig und dämpfen die Funksignale sehr stark – vor allem bei 868 MHz«, erklärt Drägers Kollege Dr. Iker Mayordomo.
Doch gerade die UHF-Frequenzen eignen sich durch ihre relativ großen Reichweiten von bis zu 15 Metern sehr gut für Logistik und Produktion. Bei für RFID schwierigen Werkstoffen, wie zum Beispiel Metallen, konnte diese Leistung daher bisher nur durch ein sehr teures Transponderdesign erreicht werden. »Die verwendeten Antennen und Transponder machen diese Spezialanfertigungen sehr voluminös. Gleichzeitig lassen sie sich nur schwer in die Faserverbünde integrieren«, schildert Dräger die Ausgangssituation. Zusammen mit Partnern aus der Luftfahrtindustrie und Forschung gelang es seinem Team nun, zuverlässige Transponder zu entwickeln, die innerhalb von leitenden und zugleich physikalisch belasteten Bauteilen einwandfrei funktionieren. Die Wissenschaftler kreierten dafür ein extradünnes Antennendesign, um die RFID-Chips auf den Werkstoffen unter einer schützenden Glasfaserschicht einbetten zu können. Gemeinsam mit Schreiner LogiData, einem Hersteller von RFID-Transpondern, hat das IIS bereits eine erste Testserie entwickelt.
Aktuell setzen sechs Prozent der deutschen Unternehmen RFID ein; vier Prozent sind es in Europa. Das ermittelte 2011 das Statistische Amt der Europäischen Union »Eurostat«. Dass dies sich bald ändern wird, davon ist RFID-Experte Maximilian Roth vom Zentrum für Intelligente Objekte ZIO, das am Nürnberger Standort des IIS angesiedelt ist, überzeugt: »Die neuen Einsatzmöglichkeiten bei den boomenden Faserverbundwerkstoffen wird die Relevanz von RFID in der Industrie weiter erhöhen. Gleichzeitig laufen aktuell einige weitere Pilotprojekte am Markt, die den Einsatz von RFID bei Logistik, Verkehr und Produktion in größerem Stil testen.« Das IIS arbeitet parallel bereits am nächsten Projekt: »SmartFiber«, das von der Europäischen Kommission gefördert ist. Die Wissenschaftler nutzen hier die RFID-Technologie, um Energie und Daten an Sensoren zu übertragen, die in Faser- materialien eingebettet sind. Diese ermöglichen beispielsweise eine durchgängige Strukturüberwachung von Windkraftanlagen.
(mb / mit einer PM des Fraunhofer IIS)
—-
Weiterführende Artikel:
– Leichtbau: Energieeffizientes Recycling von Carbonfasern aus Verbundwerkstoffen entwickelt
– Leichtbau auf dem Weg in die Großserie – erstmals automatisiertes Carbon-Fertigungsverfahren
– Faserverbundwerkstoffe für die Großserie
– Carbon-Studie: Kosten sinken bis 2020 um 30%, Faserverbundmarkt wächst jährlich um 17%
– Aluminium oder Composites – wer wird Leichtbauwerkstoff Nummer eins?
– Boeings Albtraumflieger 787 Dreamliner mit neuen Problemen
– Interview mit Prof. Dr. Rommel zum Carbon-Recycling und zum AUGSBURG Innovationspark
– Interview mit Prof. Dr. Loidl zum AUGSBURG Innovationspark (Präsident der Universität)
– Weiterentwicklung bis zur Marktreife gesucht: Verschleißschutzschicht für Faserkunststoffverbunde
—-